怎样解决压铸件缩孔
压铸件在凝固过程中会发生体积收缩,形成缩孔、缩松;因铸件内部收缩,铸件表面上会出现缩凹缺陷(见例图)。对于压铸件来说,特别是厚大的压铸件,缩孔、缩松是普遍问题。本课题从如何对合金液的收缩进行补缩,如何阻碍合金液形成集中缩孔以及如何防止产生气体、包卷气体,如何排气等几个方面进行分析研究。以消除或减少缩孔、缩凹缺陷,从而提高压铸件的良品率。
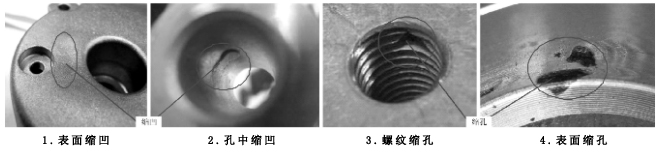
例图
1、铸件结构改进
铸件的壁厚越厚或热节越大,休积的收缩量越大,就越难以把气体排出,因此容易形成大的缩孔。这就要求尽量消除或减小铸件的热节,把铸件热节部位尖角改为圆角;铸件的壁厚要均匀,在铸件壁厚相差较大的连接处,要逐步平缓过渡;如果铸件设计不可避免热节、凸耳、凸台等,则可采用空心结构、筋条结构等来消除热节和减轻铸件质量。
铸件上较大的热节部位、宽大的平面部位容易产生表面处理铝合金压铸工艺 铝合金压铸件涡流,因而容易包卷气体;金属液难以 充填到模具深腔,铸件的盲孔、死角部位难以排气、容易包卷气体、易出现缩孔、缩凹缺陷 。设计该类铸件时,就要考虑设置内浇口和溢流排气口的位置。
2、压铸模结构改进
如果内浇口截面积过小,会导致金属液充填速度过快而产生喷射,促使金属液包卷大量的气体。因此要适当加大内浇口的截面积,防止内浇口的金属液过早凝固,从而堵塞增压补缩通道,要增强内浇口补缩能力和延长补缩时间。如果内浇口的位置距离出现缩孔、缩凹的热节位置比较远,需适当改变合金液导入内浇口的位置、内浇口的数量和内浇口进入型腔的方向,以便合金液在型腔内有序充填、压力有效传递、型腔气体有效排除,达到对热节进行有效补缩的目的。
合理设计内浇口与型腔连接的结构形式,达到理想的内浇口导流方向。要使合金液首先充填深腔、薄壁、需要较多合金液的位置、大平面的中间位置、铸件表面质量要求较高的位置、以及难以成形的位置等,使金属液在型腔内有序充填,防止金属液产生涡流和卷气。消除或减轻金属液对型壁的正面冲击,可以降低冲击部位的模具温度。注意改变内浇口的流向或位置时,要防止金属液过早凝固以致堵住分型面或排气道。
比较小的热节和非厚壁部位,可以设置在距商内浇口较远的位置,让这些位置由一些较低温度的合金液充填,这样不会导致该部位的模具温度过高。如在模具较深的型腔、死角、型腔中部等部位无法排气或排气不畅,可以采用排气塞、顶杆、模块镶拼结构排气;用点冷却加速厚壁部位合金液凝固速度;用点加热提高薄壁部位模具温度,使压力有效传递;用改变充填流向消除涡流卷气,以减小甚至消除铸件缩孔。合理设置溢流槽、排气槽位置、数目及尺寸,可以消除排气不良的现象。
尽量减小机械加工余量;要使用型芯、抽芯铸造出螺纹孔的底孔。如果压室具有较小的充满度,使用较低的压射速度和足够的压射比压,可以减轻压铸件的缩孔和缩凹。要选用合适的压射室直径,控制压射室充满度在30%-55%之间。
压铸件表面出现的轻度缩凹、粘模脱皮、小气泡等缺陷,可以通过对模具表面进行喷丸、放电或打磨处理,使模具的表面变得粗糙,这样有助于气体排出,还可以增大模具的导热效率,提高模具对合金液的冷却速度。
如果模具的冷却水管道距离内浇口太近,由于内浇口处的模具温度过低,会导致内浇口过早凝固,要使用冷却水和模温机,合理调节模具各部位的温度。
如果模具温度过高,虽然有利于补缩压力传递,但会减缓合金液的凝固结晶速度,使热节处形成较大缩孔。这就要在模具的横浇道、内浇口附近的型腔位置、型芯的高温部位,以及铸件的热节部位,给模具内部设计管道通冷却水进行强制冷却。压铸时对模具表面要多喷涂料及多吹气冷却,以降低模具过热部位的温度。
提高模具对合金液的冷却效率,使合金液内部和外部接近于同时凝固,让合金液达到快速冷却的效果,从而防止出现集中缩孔。
如果模具温度过低,虽然能加快合金液的凝固速度,能消除或减小热节处的凝固缩孔,但会过早地封闭补缩压力的传递通道,影响补缩效果;也不利于涂料中水分快速去除,增加了合金液包卷气体的几率。这时在远离内浇口的热节处不仅容易形成较大的缩孔,而且在铸件内部也会存在大量的气孔,因此,要求在设计横具时,要提高远离内浇口处、铸件薄壁处、型腔深腔处、非主杆充填型腔处模具的温度。一般是采用增加溢流槽的数量或增大其体积,电加热管加热,或模温机通热油等方法加热模具。
为了消除热节设计的铸件空心结构,在模具上设置凸台。起模斜度不能过大,否则会减小消除热节的效果。另外,如果横具使用中变形,产生了凸起部分,导致铸件表面凹陷的,只要检修模具、消除模具缺陷即可。
3、压铸工艺和合金熔炼改进
提高压铸机的压射充填压力和增压补缩压力,加大增压阀的开度(缩短增压的升压时间),这样可以及时进行增压补缩,可以增加合金液的流动补缩能力,提高铸件组织的致密度,可以通过降低低速、高速的压射速度,推迟高速的开始位置来减少金属液包卷气体的含量。还可以采用很高的高速速度,使内浇口速度达到60-120 m/s,让金属液呈雾状喷射充填型腔,这样虽然增加了铸件中气体的总含量,但不会包卷较大的气泡,能明显减小缩孔和缩凹尺寸,达到孔穴尺寸不超标的目的。试验得知,充填速度低会出现大气孔,但数量少,总量也少;充填速度高,出现气孔的数量多,总量也多,但尺寸小。
较高的低速速度,不平稳的低速速度,以及过早开始启动高速速度,都会使金属液在压射室及横浇道里出现紊流而产生卷气。压铸合金熔化或浇注温度越高,引起合金内部吸气越多、铸件结晶的晶粒越大,合金液凝固后的收缩率越大。在合金液的熔化和保温过程中需控制合金液的温度不要过热,并要使合金液处于高温的时间不要过长。
如果合金液需要超过2h的停产保温, ADC12铝合金的保温温度要降至620-630 ℃。在保证铸件不产生冷隔、浇不足的前提下,要尽量降低合金液的浇注温度,这样可以减少合金液的收缩量和含气量。
空气中的水分、炉料中的水分和油污里的有机物等,在高温时会分解出氢原子。 Al、Zn、Mg等合金液,随着温度的升高,会吸附溶解更多的氧原子。同时在合金液的氧化夹渣和夹杂物团粒中,也容易吸附氢原子,在合金液凝固的过程中,会使附着的氢原子自动脱离凝固体而进入到液体之中。当液体之中的氢原子聚集富余之后,由于温度降低,氢原子相互结合形成氢气富集的氢气产生膨胀压力,又促进了液体的补缩流动,同时也促使合金液中形成较大的气缩孔。因氯原子会附着在氧化夹渣和杂质上,仅靠除气精炼解决不了,还要仔细地对合金液进行彻底的除渣精炼操作,这样才能较好地降低合金液的含气量和杂质含量。
合金液中某些化学成分如果超差,会增大合金的体积收缩率,如铝合金中的Zn含量增加就会增大合金的体积收缩率,因此要对合金液进行常规检查,控制、调整好化学成份,并适当地控制回炉料的用量比例。
用密度检测仪检测样块,并观察样块的凝固凹陷程度,观察合金液的收缩量和含气量。一般结晶温度范围大的合金容易出现集中缩孔,其铸件容易出现漏气,而一般结晶温度范围小的合金,则容易出现分散的缩孔,其铸件不容易出现漏气。为了提高铸件的密度,可以对合金液进行变质处理,在铝合金液中添加0.15%-0.20%的Ti、Sr等晶粒细化剂,能减轻合金的缩孔倾向。必要时就需要改用体收缩率、线收缩率小的合金品种。
如果铸件的内浇口断面出现缩孔、影响因素较多。解决的方法有:
为使压力更好地传递,适当改进浇注系统,加大内浇口截面积,加大内浇口厚度,防止因内浇口过早凝固而影响压力的传递;如果横浇道比内浇口冷却收缩快,会使内浇口处金属液倒流到横浇道,结果使铸件在内浇口处形成缩孔,这时就要减小内浇口厚度,给内浇口部位进行充分冷却;提高增压压力;消除金属液在压射时产生的飞料和飞边毛刺;加大增压上升速度阀的开度;延长增压持压时间到浇口完全凝固为止;对金属液精炼处理减少含气量,降低金属液的浇注温度,减少金属液的收缩等,这些都可以减小或消除内浇口处的缩孔。
采用半固态压铸工艺,该工艺是将具有固相率3%-50%的合金浆料,压射充填到型腔内,虽然在合金浆料内部已经有固相颗粒存在,能够加速合金凝固,消除大的缩孔,但因为还有部分处于液态的合金,在结晶时存在体积收缩,最终还会出现小的缩孔或缩松,不过,半固态压铸比液态压铸出现的缩孔、缩松尺寸小,数量要少很多。
4、压铸操作改进
压铸的余料料饼厚度过薄,会影响增压压力的传递,使压射最终的增压起不到有效的补缩作用,所以要采用定量浇注,确保压铸的料饼厚度。给型腔喷涂脱横剂的量过多,涂料发气量大,涂料浓度高,涂料的水分在浇注前未蒸发干净,都会促使产生大虽气体卷入金属液,如果气体被压缩在型腔表面与金属液界面之间,在铸件皮下出现大的气孔,在铸件表面就会出现缩凹。
受到涂料的氧化、污染的气缩孔、空穴的内壁表面多呈暗灰色。这就要求涂料的浓度低、用量少、喷涂均匀;喷涂料后要用压缩空气把型腔表面的水分吹干。让水分挥发干净后再合模;提高模具温度,使涂料水分能多快速地蒸发掉;必要时,还可以改用发气小的涂料。
无论是油剂、水剂或固体颗粒状的冲头润滑涂料,如果使用量过多,都会在遇到高温合金液时产生大量气体,部分气体进入金属液后不能及时排出;未燃烧尽的涂料微粒进入合金液后,还会继续燃烧产生气泡微粒。气泡微粒与合金液混合,更难以排出。所以一定要定时点检,控制好冲头润滑剂的用量。
如果内浇口的断面有气孔或有灰黑色、黄黑色的夹渣,是冲头涂料、模具涂料、冲头漏水等遇到金属液后在压射室产生大量的气体和氧化夹渣进入合金液,污染了压射室里的合金液,使金属液含有大量的气体,特别明显的表现是在压铸件内浇口的断面会呈现气孔和氧化夹渣,在整个铸件的内部断面,也会呈现这些缺陷。
其关键的原因:
一、冲头涂料太多
二、是冲头漏水到压射室
三、是横具涂料水喷进了压射室里,所以一定要定时点检,不让压射室里进入水分
如果铸件表面上呈现松散不紧实的宏观组织,这时在热节处出现缩凹。这是因为模具的温度太低,需要适当提高模具温度和合金液的浇注温度,减少涂料的用量,提高压射比压,或是因为型腔喷涂涂料后,多余的涂料水分没有吹干,型腔中产生了大年的气体所致,同时铸件表面还会发黑。
对出现缩孔、缩凹部位的模具表面,可以用多喷涂涂料来降低模具局部的温度;也可以用冷却水管、定点定时地对模具的局部表面喷洒冷却水,来降低模具的温度,但容易引起模具寿命缩短。
如果模具表面或型芯表面,受到合金液的冲击而过热,或在铸件的热节部位而过热,模具表面会粘一层压铸合金,这层压铸合金会阻碍金属液在结晶凝固时热量的快速散发和传递,增加了铸件出现缩孔、缩松的几率。
这时除了清理、抛光模具表面粘结的合金、对模具进行氮化处理之外,关键是要在模具过热部位设置冷却水管道,通水冷却来降低过热部位的横具温度。
5、强制补缩法
强制补缩是使用外力推动液态、半固态及固态的金属移动进行补缩。外力实现铸件的强制补缩有两种方法:
1.局部挤压
2.锻压补缩
采用先压铸充型,后挤压补缩或模锻补缩的工艺,是解决铸件缩孔、缩松缺陷的有效途径。在压铸工艺的基础上,增设强制的局部挤压补缩,是能够与压铸工艺特点相适应的,能很好地解决压铸件局部的缩孔、缩松问题。
6、结语
缩孔、缩松缺陷,主要是由于合金液结晶时的体积收缩,合金液中包卷的气体和合金液溶解的氢原子析出后的气体形成的,主要的措施是要设计出没有热节的、易于充填的铸件;设法加快合金的收缩,降低热节部位的模具温度;精炼合金液,减少合金液充填型腔时包挤压铸造是在外挤压力下凝固的近净成形工艺。
外挤压力可以促使凝固的铸件与模具紧密接触,增加了铸件/模具间的传热,从而得到组织细化和枝晶间距较小的凝固组织,使铸件具有良好的力学性能,因此,该工艺也特别适用于高品质的安全结构件的生产。
在挤压过程中,外挤压力不仅改变了铸件/模具界面的接触情况,而且改变了液相线温度。从而改变了铸件的传热与温度分布。同时,固相形成和凝固收缩对来自冲头的压力传递也具有重要影响,因此,热力相互作用行为是挤压铸造的本质问题之一。对此,一些研究者利用数值横拟方法进行了研究,但是,由于高温和外力作用下型腔内压力测试的难度与复杂性,仅压铸过程压力变化的测试与分析有少量报道,而挤压铸造相关研究工作尚未见报道,因此,已有数值模拟研究只能通过缩孔缺陷进行间接验证,缺少试验压力测试的直接对比。
『不是原创,来自于互联网』